Mission Update: Engineering at the Frontier
Whether it’s working with NASA to build on the Moon or advancing manufacturing here on Earth, our focus is solving the hardest problems in environments where failure is not an option. SpaceFactory exists to extend human capability into places where conventional tools and systems cannot go, building the technologies that make life and work possible on the frontier.
Our expertise lies in advanced manufacturing: engineering that blends materials science, digital design, automation, and real-time data to produce faster, lighter, and smarter than traditional methods allow. We are pioneering large-scale 3D printing for space applications and extending that capability into ruggedized, expeditionary platforms built to deliver resilience in the most austere conditions.
What defines SpaceFactory is our willingness to take on the hardest problems—to boldly build where no clear path exists. Our innovations bridge Earth and space, grounded in rapid prototyping and agile development. Unencumbered by convention and undaunted by the unknown, we are engineers of the frontier.
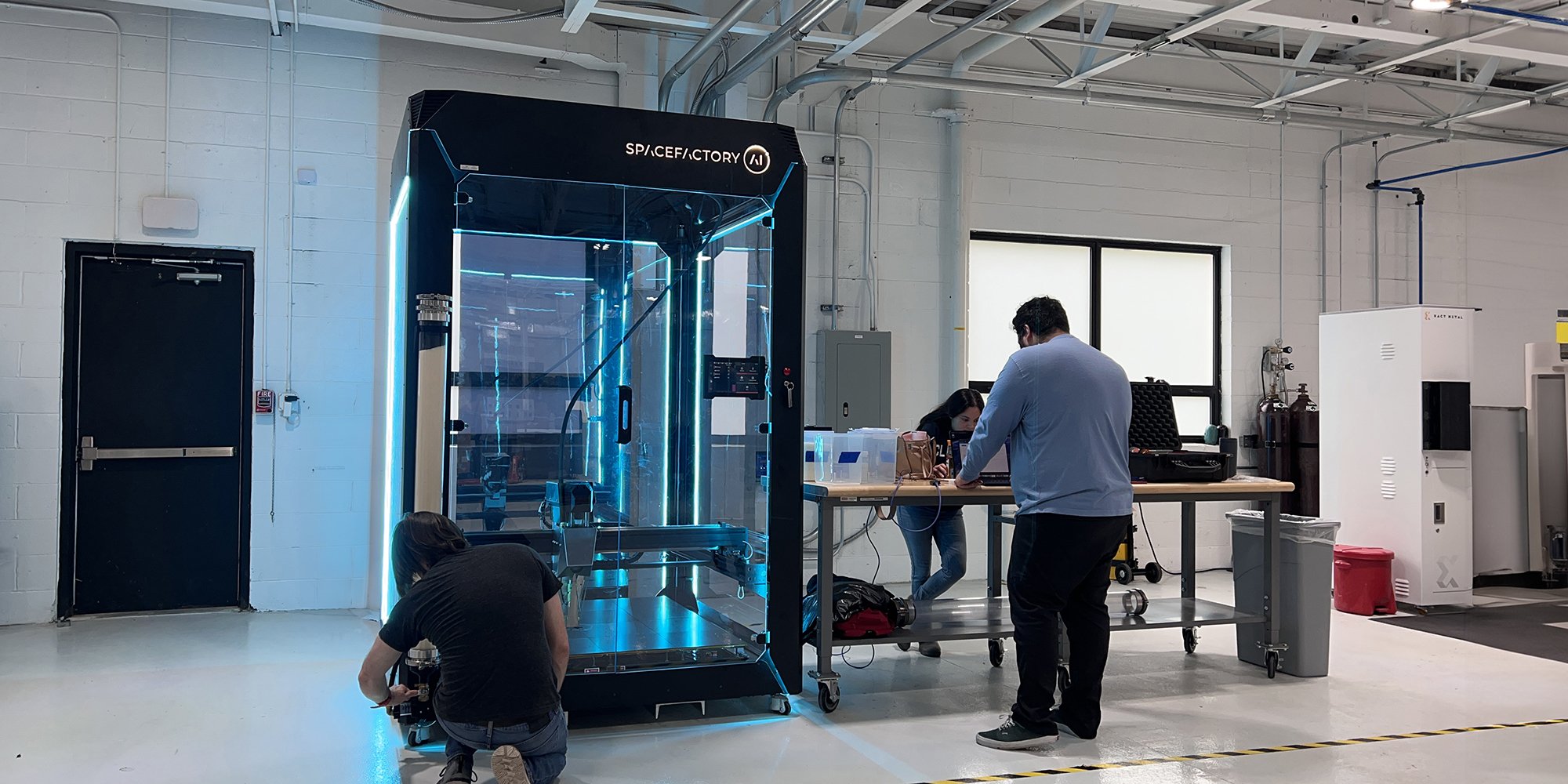
Helping Local Businesses Respond to Tariff Challenges
We are calling on Huntsville, AL area businesses interested in exploring 3D printing solutions to participate in a pilot program we have launched in response to tariff challenges. Starting with a free consultation, if your application is a match for our capabilities, we will provide no-cost design for additive manufacturing services and work with you to build a prototype and set up a pathway to full-scale production. See details below.

Lunar Inroads
In a milestone in space construction technology, SpaceFactory and Michigan Technological University (MTU) successfully built and tested the first-ever lunar 'road' in a simulated space environment, replicating the dusty vacuum conditions of the moon. This pioneering project not only demonstrates the viability of constructing durable infrastructure on the lunar surface but also underscores the powerful synergy between the private sector and academic institutions in advancing space technology.
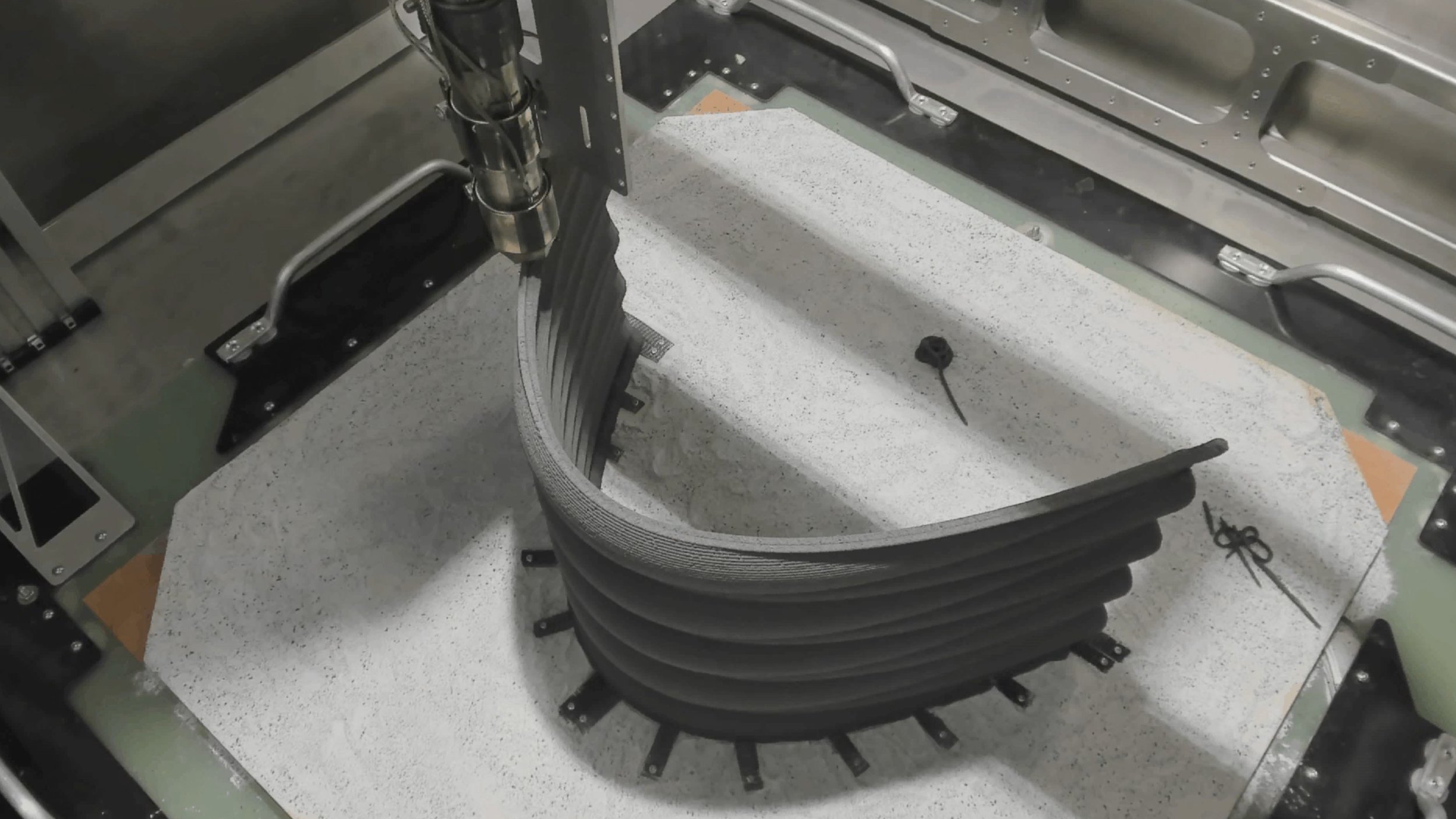
Lunar 3D Printing Milestone Achieved
In a historic first, SpaceFactory and NASA Kennedy Space Center partnered to perform the first-ever 3D printing in a freezing vacuum, emulating the harsh conditions found at the Moon’s south pole. This initiative successfully demonstrated 3D printing technology at the extreme temperature of -200°C using a lunar simulant and biopolymer matrix. The experiment validates the feasibility of constructing with lunar resources in such extreme environments, paving the way for future lunar habitats and infrastructure.
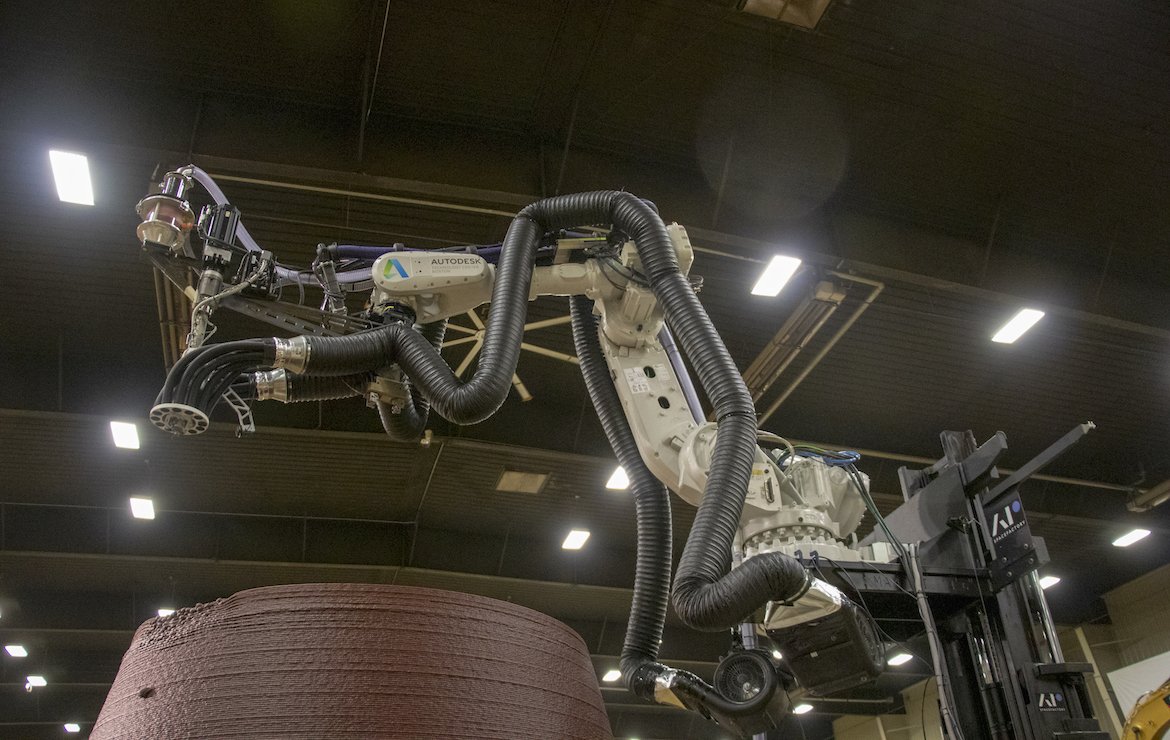
Reflecting on Our Roots: The NASA Centennial Challenge
SpaceFactory's journey began as a bold venture into the uncharted territories of large-scale additive manufacturing and extraplanetary construction with our groundbreaking project, 'MARSHA' (Mars Habitat). As a small startup, we dove head-first into the NASA Centennial Challenge, pioneering the use of a composite basalt-fiber and biopolymer to 3D print habitats designed for Mars. Winning this challenge was just the beginning.
-
AI SpaceFactory was founded in February 2017 by a team of architect and engineers to enable human habitation beyond Earth, and to apply those technologies to improve how we build and live on our planet. That same year, we embarked on the multi-phase NASA Centennial Challenge to develop the design and technologies to build on Mars—a challenge we ultimately won in May 2019.
-
AI SpaceFactory entered NASA's 3D Printed Habitat Challenge in its third and final phase which required the design and construction of a prototype Martian habitat. Through the challenge, we began to push the thresholds of what's possible within 3D printing technology and materials.
NASA CENTENNIAL CHALLENGE - DESIGN PHASE 2ND PLACE WINNER
SpaceFactory was one of five designs selected from a field of seventeen teams due to our innovative design born from the Martian environment. Our Mars habitat, MARSHA, marks a radical departure from previous habitat designs. MARSHA stands upright and tall on the Martian surface with highly human-centric, habitable spaces tuned to the demands of a Mars mission.
NASA CENTENNIAL CHALLENGE - 1ST PLACE WINNER
AI SpaceFactory was announced the ultimate winner of the NASA 3D Printed Habitat Challenge, receiving a $500K award to seed future research and development. Our 15-foot tall prototype was commended for its high degree of autonomy and use of a recyclable biopolymer 3D print material that withstood NASA’s pressure, smoke, and impact tests better than its concrete competitors.
-
AI SpaceFactory began the TERA (short for Terrestrial Analog) project to validate our space-technologies on Earth. An eco-friendly 3D printed dwelling made entirely with sustainable materials, TERA proves that revolutions in technology, artificial intelligence, and robotics can reduce waste and our collective carbon footprint through Space-driven construction.
-
SpaceFactory was one of 17 companies selected by NASA to co-develop lunar technologies under the Announcement of Collaboration Opportunity (ACO) program alongside Blue Origin and SpaceX.
The partnership between SpaceFactory and NASA Kennedy Space Center’s “Swampworks” successfully advanced lunar 3D print technology through testing in a vacuum chamber at temperature as low as -200°C using a regolith-polymer feedstock which could be produced locally on the Moon.
By 3D printing in a lunar-like environment, SpaceFactory and NASA made significant strides in maturing our technology for a possible lunar surface demonstration within the decade. -
In January 2023, SpaceFactory launched our pilot robotic arm 3D printer, ASTRA. Building on the prototype developed for the NASA Centennial Challenge, SpaceFactory engineered ASTRA for scale, simplicity, and sustainability. ASTRA’s mission is to enable the next generation of builders and creators through its use of recycled 3D print materials, automated tool-path algorithms, and user-friendly interface.
Starting September 2023, SpaceFactory will launch a series of large format gantry-style 3D printers which leverage technology developed through our NASA partnership. Beginning with the T200 “Starforge”, these modular printers are designed to help a wide spectrum of industries in producing intricate parts, streamlining operations, and unlocking unparalleled efficiencies in their processes. -
In partnership with Michigan Technological University (MTU), SpaceFactory set out to explore not only methods of building with bulk regolith, but developing novel materials and robotic systems to perform construction activities.
Unlike regolith-polymer composite 3D printing, these mass regolith infrastructures (MRIs) contain only 0.5-2.0% non-regolith mass yet can achieve over 150-times the strength of unstructured regolith. Through low-energy, low-mass applications, our research into MRIs is grounded in near-term, essential surface enhancements to support lunar launch-land, mobility, power, and communication systems.
In a short span of nine months, SpaceFactory developed several patent-pending technologies around building MRIs including constructing the first-ever lunar “road” in vacuum.