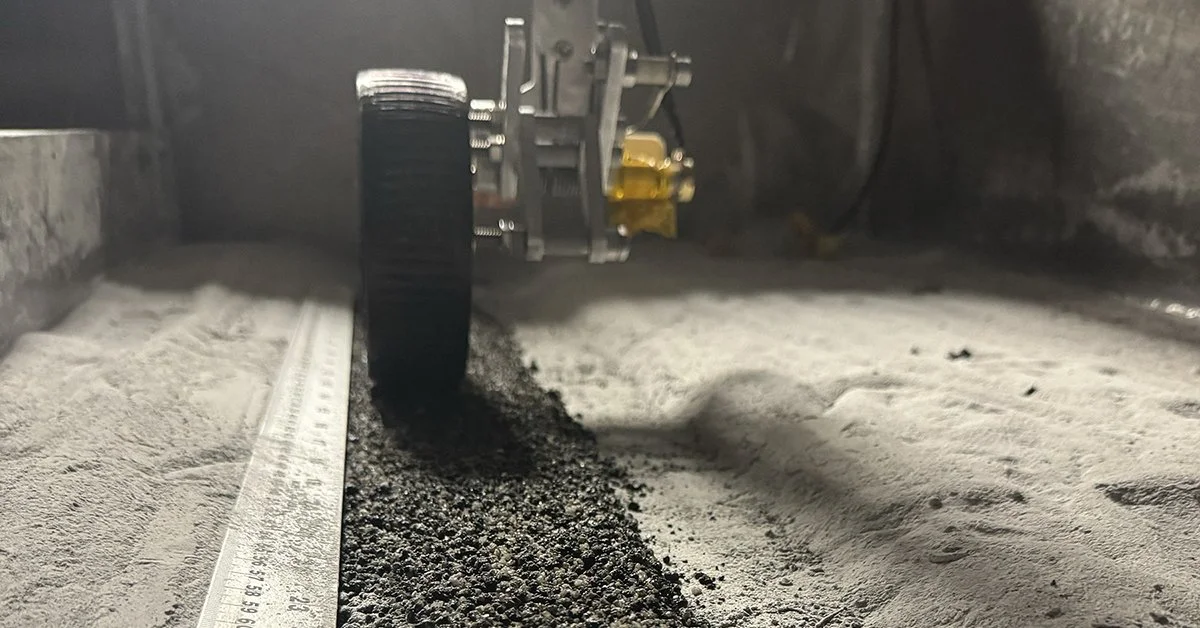
Lunar Inroads
PAVING THE FUTURE OF LUNAR TRANSPORTATION
LUNAR ROAD
Our groundbreaking partnership with Michigan Tech advances lunar infrastructure technology with the first-ever road built in a simulated space environment.
In a milestone in space construction technology, SpaceFactory and Michigan Technological University (MTU) successfully built and tested the first-ever lunar 'road' in a simulated space environment, replicating the dusty vacuum conditions of the moon. This pioneering project not only demonstrates the viability of constructing durable infrastructure on the lunar surface but also underscores the powerful synergy between the private sector and academic institutions in advancing space technology. The project was made possible through a NASA-funded Phase 1 STTR partnership.
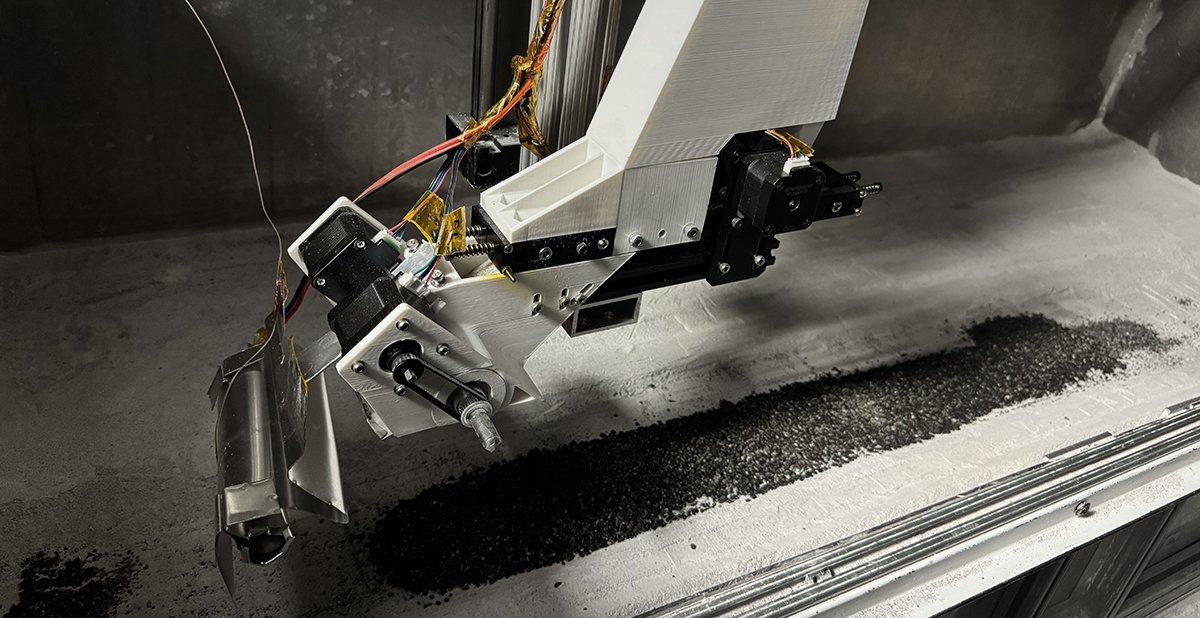
HOW WE DID IT:
LEVERAGING IN-SITU RESOURCE UTILIZATION (ISRU)
The SpaceFactory-MTU project brought forth several innovative engineering strategies designed to maximize the utility of lunar regolith, an abundant resource on the moon's surface. A key innovation lies in the development of a novel material, referred to as lunar 'asphalt,' engineered specifically for the lunar environment using regolith and biopolymers. The process was carried out by a robotic apparatus that performed the construction tasks in vacuum, laying and heating the lunar asphalt into a dense, cohesive surface capable of withstanding the mechanical stresses of lunar vehicle traffic. The team demonstrated the material's durability by driving a simulated lunar rover wheel over the road 900 times, covering 720 meters. Significantly, the durability test revealed no dust accumulation on the wheel, highlighting a significant advantage of our patent-pending technology.
WHY DO IT?
REDUCING THE COST AND RISK OF LUNAR MISSIONS
As on Earth, roads on the Moon will reduce wear-and-tear on vehicles, allowing them to be lighter, faster, and longer-lasting.
Lunar dust, or regolith, is notoriously problematic in lunar environments due to its fine, jagged particles that adhere to surfaces, infiltrate machinery, and obscure sensors, compromising equipment functionality and longevity. Additionally, the moon's lack of atmosphere, reduced gravity, and the electrostatic properties of the dust mean it can remain airborne, posing health risks to astronauts and contaminating habitats. Paved surfaces not only enhance the operational integrity of lunar vehicles and systems but also significantly boost the safety of long-term lunar habitation and exploration.
By driving on paved tracks, a rover’s mass and complexity can be significantly reduced by downsizing its motors, wheels, and suspension components, and simplifying its navigation and dust mitigation systems. With reduced wear-and-tear, repairs and replacements will be less frequent. These factors translate to both capital and operational savings which we estimate at 50% or more over the course of a long-term mission.
WHAT’S NEXT?
BUILDING THE FOUNDATION FOR LONG-TERM SPACE EXPLORATION AND HABITATION
The lunar road is just one example of the partnership’s broader investigation into foundational lunar construction technologies. Drawing on SpaceFactory’s expertise in terrestrial construction, the team developed specialized geogrids that increase the strength of regolith-based structures over 165-fold, with the geogrids comprising only 1-2% of the structure’s total mass. This innovation, which applies to both roads and three-dimensional structures, demonstrates the potential of In-Situ Resource Utilization (ISRU) to reduce the launch mass and cost of lunar shelters by over 80%, a figure calculated through detailed testing and simulation. By using local materials and minimal Earth-supplied additives, SpaceFactory’s approach proves that lunar infrastructure can be both material- and energy-efficient, providing stable, dust-free environments that reduce maintenance and extend the operational lifespan of space exploration systems.
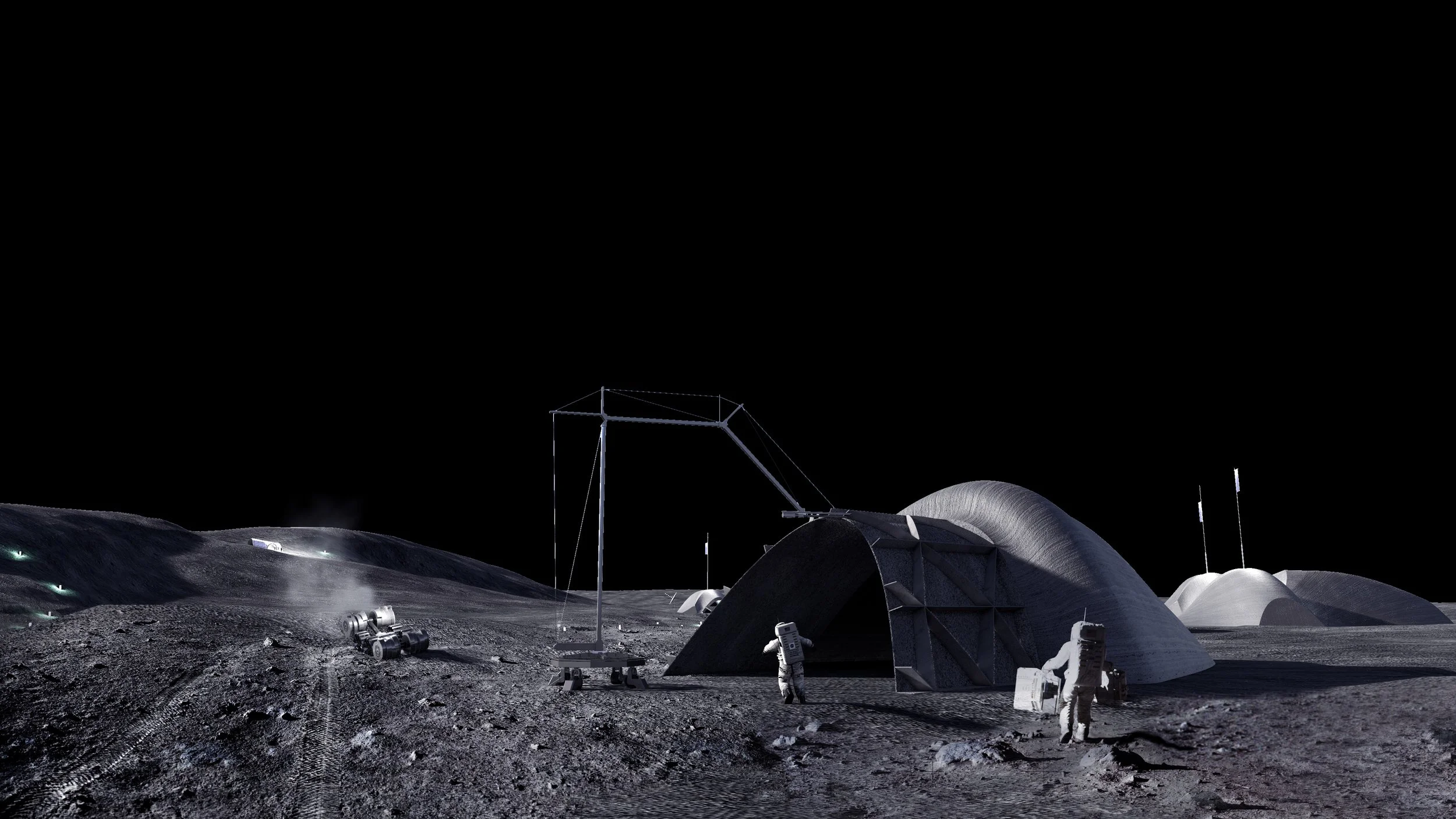
Building on the project’s initial successes, future work is designed to push the technology readiness levels further in preparation for a lunar surface demonstration. The next phase aims to complete a fully integrated construction system, ready for lunar deployment, with the capability to construct both roads and additively manufacture three-dimensional structures—paving the way for sustainable, long-term infrastructure on the Moon and Mars.